Design for manufacture and product testing
When designing a new product it is critical to have a good understanding of the manufacturing process, in this instance plastic moulding. The most common would be injection moulding, but we have been involved in all aspects of this industry, covering injection moulding, blow moulding, and rotational moulding. We have seen many instances of great concepts and aesthetics but no consideration given to the reality of manufacturing the parts cost effectively.
This is where we have excelled, being able to retain initial design intent and functionality, but reworking this, to enable the project to move forward to production.
You can send us CAD files in most formats, we run Fusion 360 and Solidworks, from these we can easily give an opinion as to the suitability of the intended manufacturing method.
Design for Manufacture (DFM)
Product Development / Evaluation
Once a product is considered suitable for injection moulding, blow moulding, or a variety of alternatives, our next considerations for the client are based on the following:
Quantities required, many customer requirements are very limited numbers, the parts concerned may be of a high value but very low numbers for production. In this case there are options available for producing inserts to go into an existing mould bases, this saves the client the cost of building an entire mould. Inserts can be made from many materials ranging from though hardened H13 steels through to aluminium. Whatever the requirements are we can offer a cost effective solution.
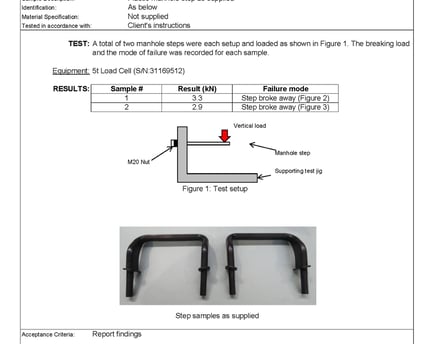
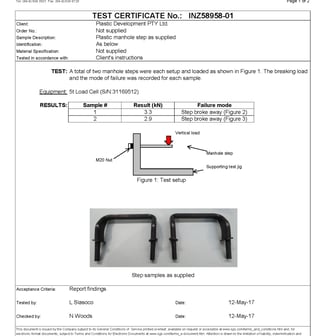
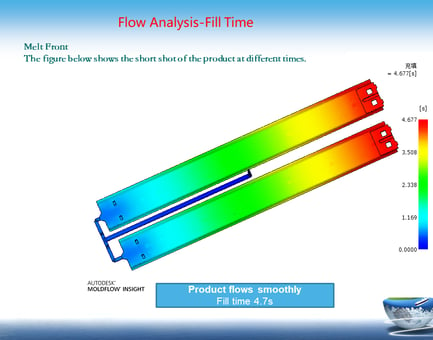
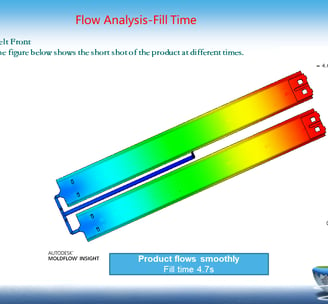